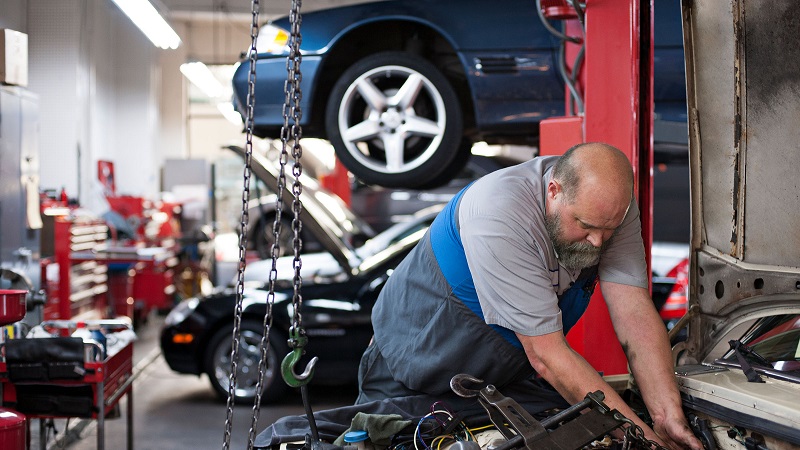
From running lift gates and cranes to even helping with steering and braking in some configurations, trucks mostly rely on hydraulic systems for several important purposes. For heavy-duty jobs, these devices are indispensable since they create notable force by pressurized fluid. Like any complicated equipment, hydraulic systems are prone to wear and breakdown, though. A hydraulic system failing might cause operations to stop, therefore endangering safety and causing expensive downtime. Experts in repairs have a sharp eye for seeing the early warning indicators and fundamental reasons of these breakdowns.
Recognizing the Warning Signs
Often first gathering information from the truck operator or owner, a skilled technician then starts their check. Typical complaints mentioned with a Heavy Duty Truck in Great Falls, MT are slow operation, difficulty lifting or moving a weight smoothly, odd noises like whining, grinding, buzzing, too much heat coming from components, or obvious leaks. These symptoms are absolutely vital signs suggesting possible problems like low fluid levels, tainted fluid, worn-out seals, internal component wear, or perhaps a malfunctioning pump. Knowing these early symptoms helps the professional focus their diagnosis efforts and narrow down the options.
The Expert’s Initial Assessment
The professional inspects a truck with hydraulic issues visually and audibly. They carefully inspect every hydraulic line and hose for wear, cracking, bulges, and abrasion, which lead to leaks. Fittings are checked for leaks and tightness. Cylinders are inspected for seal leakage, dents, and scratches. The hydraulic fluid reservoir is checked for debris, cloudiness or showing water, and discoloration in addition to level. Activating components and listening to the pump can reveal cavitation, aeration, or pump damage sounds.
Beyond the Surface: Diagnostic Tools
Although visual and aural tests are important, professionals probe farther with specialist diagnostic instruments. System pressure is measured at several sites and load circumstances using pressure gauges; values are compared against manufacturer standards to find problems with the pump, relief valve, or internal component leaks. Often suggestive of either too great friction, internal leaks, or fluid breakdown, temperature sensors can identify overheating problems in the fluid, pump, or lines. Laboratory analysis of fluid samples might reveal contamination by water, air, or metallic particles, which accelerate wear and component failure.
Conclusion
What repair professionals search for goes beyond simply spotting the obvious issue; they also look for the underlying cause and weigh preventative action. A more robust repair results from knowing why a seal failed, why the fluid is contaminated, or why a pump is noisy. The best approach to avoid expensive hydraulic system failures is, they realize, consistent preventative maintenance involving timely fluid flushes, filter replacements, and routine hose, fitting, seal inspections. Combining operator reports, thorough inspections, and modern diagnostics guarantees truck hydraulic systems are dependable and safe.